35 Years of Metal Forming Experts, From Concept to Craft: Your Forge Partner.
“Precision Forged, Powering Progress”.
Who Are We ?
We deliver precision-forged components for mission-critical systems across automotive, aerospace, and industrial engineering sectors. Leveraging state-of-the-art manufacturing infrastructure and application-specific engineering, our components achieve reliability parameters that meet or exceed ISO 9001 specifications.
Where Are We
Timeline
Services
Design to Delivery Solutions for Forging & Machining
We specialize in providing ODM and OEM services for precision forged metal components and machined parts. Leveraging advanced forging technology, CNC machining capabilities, and a customer-centric approach, we deliver tailored solutions that meet global standards for industries.
Why Choose Us ?
- End-to-End Service: From design to after-sales support.
- Flexible MOQ: Support both small-batch prototyping and mass production.
- Competitive Pricing: Optimized supply chain and lean manufacturing.
Design & Engineering Support
Collaborate with our R&D team to customize product designs based on your technical specifications, functional requirements, or prototype samples. We optimize forging processes and material utilization to enhance performance and cost-efficiency.
Material & Process Selection
- Material Expertise: Aluminum, Carbon steel.
- Forging Techniques: Hot forging, cold forging, precision die forging, and isothermal forging.
- Machining: CNC turning, milling, grinding, and surface treatment.
Size & Tolerance Customization
Produce components with custom dimensions (from micro-parts to large-scale forgings) and strict tolerances (ISO or ASME standards). Our precision-controlled processes ensure consistency for high-volume production.
Certification & Quality Assurance
- Certifications: ISO 9001.
- Testing: Fluorescence testing, X-ray testing, hardness testing and metallographic analysis.
Packaging & Logistics
Design protective packaging (e.g., anti-rust films, wooden crates) and offer global logistics solutions (FOB) to ensure safe delivery.
All-in-One Solution: Empowering the Entire Process From Concept to Delivery
- Design support: Provide DFM (manufacturability analysis) and 3D simulation.
- Prototype development: Deliver the first piece within 30 days and support functional testing.
- Batch production: Flexible production line supports 2000-50000 orders
Equipments & Technique
- 7 Servo-Electric Screw Press Forging Line.
- Automated Heat Treatment line.
- Machining Center.
- Automated Acid Pickling Line.
- Precision Forging: Near net forming technology, material utilization rate increased by 30%.
- Isothermal Forging: Improves grain uniformity by 30%
- Heat Treatment Process: uniform temperature quenching+cryogenic treatment, hardness uniformity ≤ 2HRC.
- Non Destructive Testing: Fluorescence testing.
- Non Destructive Testing: X-ray testing.
- Hardness & Performance testing
- Grain size detection
Materials & Standards
ASTM | DIN | GB |
---|---|---|
Grade: 6061 Standard: ASTM B209 |
Grade: EN AW-6082 Standard: DIN EN 573-3 |
Grade: 6061 Standard: GB/T 3190-2020 |
ASTM | DIN | GB |
---|---|---|
Grade: 7075 Standard: ASTM B209 |
Grade: EN AW-7075 Standard: DIN EN 573-3 |
Grade: 7A09 Standard: GB/T 3190-2020 |
ASTM | DIN | GB |
---|---|---|
Grade: 6063 Standard: ASTM B221 |
Grade: EN AW-6063 Standard: DIN EN 755-2 |
Grade: 6063 Standard: GB/T 5237-2017 |
ASTM | DIN | GB |
---|---|---|
Grade: 5083 Standard: ASTM B209 |
Grade: EN AW-5083 Standard: DIN EN 485-2 |
Grade: 5083 Standard: GB/T 3190-2020 |
ASTM | DIN | GB |
---|---|---|
Grade: 2024 Standard: ASTM B209 |
Grade: EN AW-2024 Standard: DIN EN 573-3 |
Grade: 2A12 Standard: GB/T 3190-2020 |
Certification
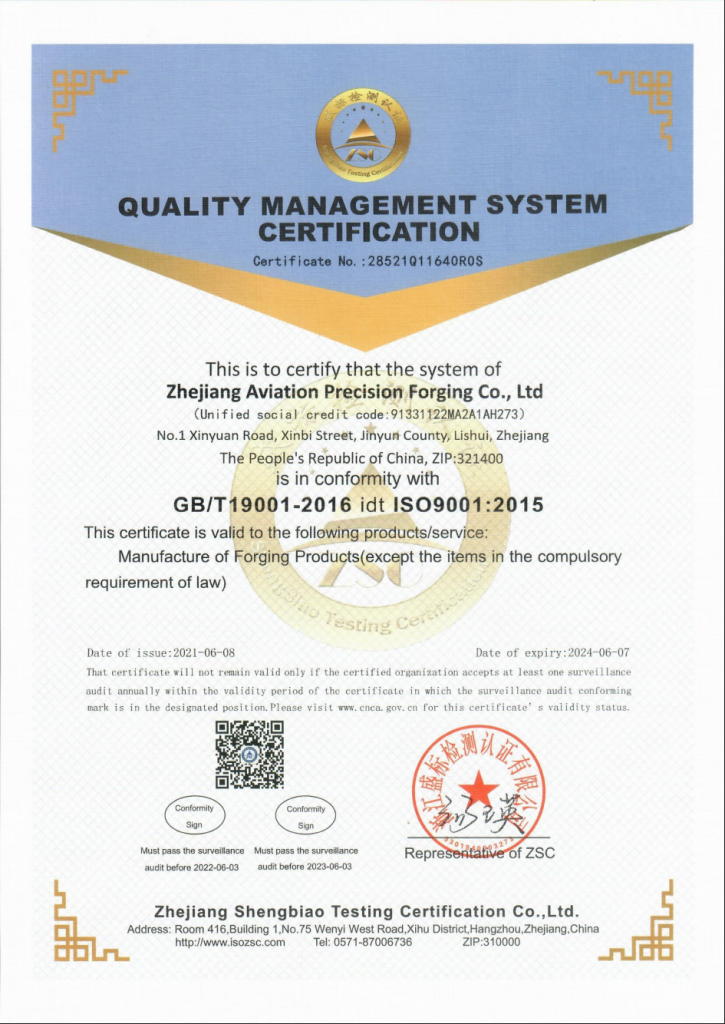
Aviaforge practice green forging through technological innovation, reducing carbon emissions by 2500 tons and saving 80000 tons of water annually. In the future, we will continue to explore zero carbon manufacturing and work with customers and communities to build a sustainable industrial ecosystem.
Closed Loop Water Resource Recycling
Compliant Disposal of Hazardous Waste
- Entrust qualified hazardous waste treatment enterprises to carry out harmless treatment of quenching oil residue and waste cutting fluid,
Green Production innovation
- Promote precision forging and isothermal forging, reduce subsequent machining volume, reduce steel consumption of individual products by 15%, and decrease energy consumption by 22%.
- A 5MW photovoltaic power station is installed on the roof of the factory area, with an annual power generation of 6 million kWh, covering 30% of the production electricity demand.